Nearly 17 billion barrels of oil have traveled through the Trans-Alaska Pipeline System (TAPS) since the first oil moved through more than 40 years ago. A key component of the pipeline recently faltered, reducing productivity, and ATS was handpicked by the operating company to get the fix delivered quickly.
The necessary parts were coming from Italy and needed to get to Alaska and the timeline was tight. ATS teams kicked into high gear to get the appropriate pieces in place to pick up in New Jersey on July 29, 2019 in order to reach the deadline of having the parts delivered to Alaska by August 8, 2019.
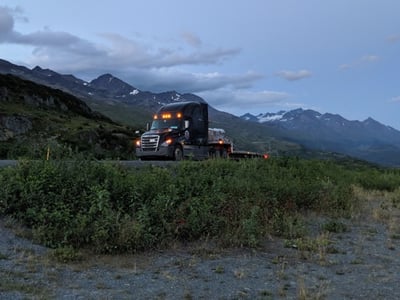
Ultimately two tractors and two trailers were needed to transport the parts to their final destination. One of the components fit onto a standard step deck trailer, while the other required a trailer that could handle a wider load. Because of the tight timeline, ATS enlisted four Drivers to work as teams in order to drive more miles
quicker.
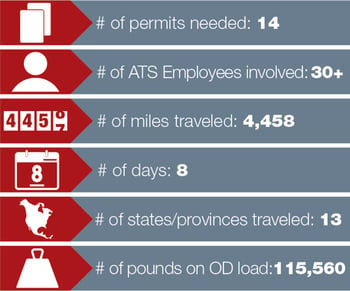
In-house permits and routing teams worked to ensure there would be no delays in the nearly 4,500 mile route, including what states and provinces allowed night time and weekend travel with an oversize load. Operations teams were constantly monitoring the two trucks to give the customer an accurate arrival time in order to have cranes ready for immediate offload.
Thanks to the teamwork of more than 30 ATS Employees, including safe Drivers who knew the geography, the vital components were delivered to the site on August 5, three days earlier than the deadline. That allowed the customer more time to test the components ahead of the planned shutdown and install.
ATS is proud of the Employees who lived the ATS values, particularly innovation, to get this job done safely and ahead of schedule. This customer needed a transportation solution that didn’t previously exist, but ATS Employees and Drivers made it possible through hard work and commitment to serving our customers with the highest level of service.